Fanuc Series 0i Manual
Designed to be extremely user-friendly, FANUC’s new iHMI makes operating CNC machines easy and efficient. The new panel is flat, features ergonomically positioned keys, completely redesigned hardware and a brand new user interface. To support seamless integration into existing machine concepts, it shares the same dimensions as other FANUC interfaces, allowing users to retain existing keypads and to switch easily from old to new hardware. Despite its redesigned look and more intuitive layout, FANUC users will find it provides a familiar user experience. For maximum machine uptime, iHMI comes with new maintenance and data logger functions required for IoT and smart factories. The CNC series 0 i model F provides the ideal basic solution for multiple control applications.
Ready to use, it boasts latest generation hardware and a complete package of standard software. To maximise productivity on more specific applications, it can be easily customised using a range of additional functions. Combining unbeatable value for money with unrivalled performance and reliability, it includes features and functions usually associated with high performance systems. Key features:.
up to 12 axes, 6 spindle axes and 2 paths. up to 2 additional loader paths. 4-axis simultaneous and 3+2 axis machining. ready to use with integrated software package. excellent performance-to-cost ratio.
integrated FANUC Dual Check Safety function. shop-floor programming via MANUAL GUIDE i or TURN MATE i. additional functions for simple customisation. integrated high-speed PMC. high speed and high quality machining package. maximum look-ahead blocks 400. common operability, maintainability, network and PMC function with CNC Series 30 i-MODEL B.
FANUC Series 30i / 31i / 32i-model B controls are ideally suited to complex high-speed, precision machines equipped with multiple axes and multi-path functionalities. To meet the needs of various types of user, 30i / 31i / 32i-model B controls combine user-friendly operation with exceptional levels of accuracy, reliability and efficiency across every perceivable kind of machine tool, including multi-axis lathes, 5-axis machining centres, gear cutting machines or transfer machines.
Key features:. up to 96 axes, 24 spindle axes and 15 paths. 5-axis machining. compound mill / turn or turn / mill machining. extended integrated preventive maintenance functions. integrated FANUC Dual Check Safety function.
shop-floor programming via MANUAL GUIDE i. collision control via 3D Interference Check.
dynamic compensation functions for highest accuracy. High-Speed Smooth Tool Center Point 5-Axis Compensation. Learning Control / High-Speed-Cycle-Machining. integrated high-speed PMC. high speed cutting. iHMI offering intuitive and extremely user friendly operation.
The FANUC series 35i-MODEL B control is primarily designed for transfer lines, gantries or multiple milling and drilling stations. More capable and robust than a PLC-based motion system, it supports the widest range of industry standard protocols including Ethernet/IP, ProfiNet and DeviceNet. 100-MBit Ethernet integration translates into low cost system interconnectivity, high-speed part program transfers, data collection and troubleshooting from remote locations. Additional software options enable fast high-precision multi-path processing and provide you with the freedom to develop unique bespoke solutions of your own. To reduce cycle times up to five independent 9.1 nanosecond-per-step PMC ladders execute simultaneously, eliminating the cost and complexity of external PLCs in many applications. Key features:.
Fanuc Series Oi-md Manual
up to 20 axes, 4 spindle axes and 4 paths. ready to use with integrated software package.
simple axis setup. additional functions for simple customisation. up to five integrated high speed PMCs. The FANUC CNC Power Motion i-A is the ideal high response CNC for efficient high performance motion control and a wide range of industrial machining applications. With capabilities including multi-axis and multi-path functionality for position, speed and torque control, it makes the ideal solution for press machines, loaders, stamping machines, wire saw, winding and filling machines to name but a few. High-level motion path programming is very straightforward, with the programming system enabling fast, low-cost application development.
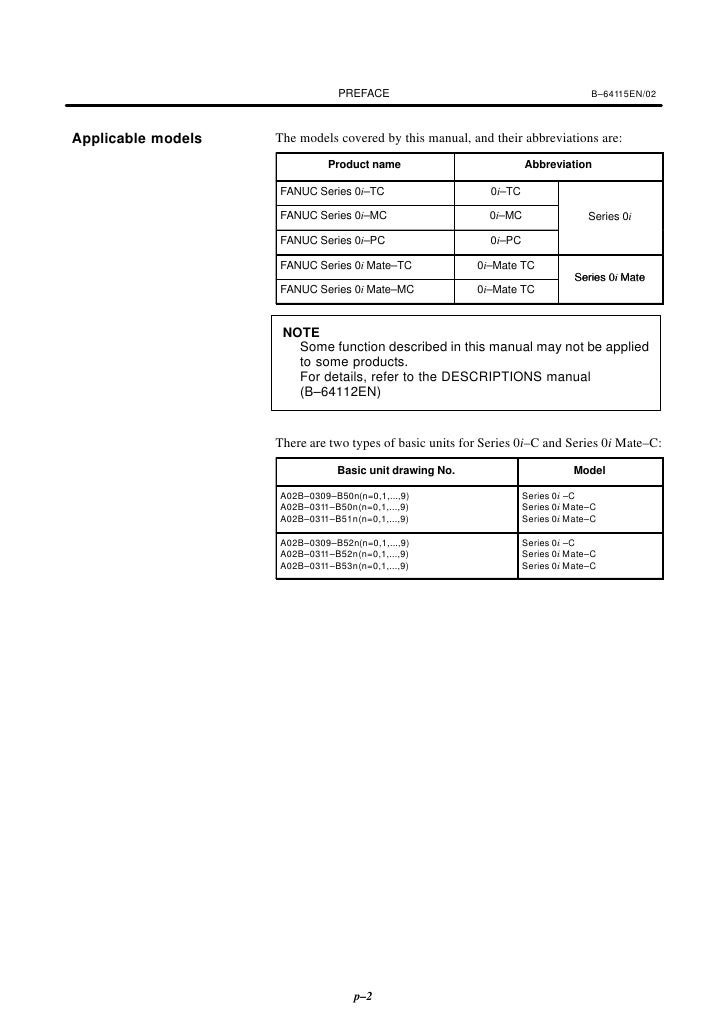
Integrated motion specific architecture translates into very competitive hardware costs for multi-axis applications. A wide variety of screens are also available for easy setup, operation and maintenance, as is screen sharing. Key features:. up to 32 axes and 4 paths. ready to use and includes an integrated software package. integrated FANUC Dual Check Safety function. additional functions for simple customisation.
integrated high-speed PMC. CAM function. perfect combination of pressure and position control.
Series 0 i-MODEL F The FANUC Series 0 i-MODEL F is the newest generation in the highly popular Series 0 i and integrates many features found on the Series 30 i-MODEL B. The Series 0 i-F brings faster, more accurate performance to a wide range of milling, turning, punching and grinding applications with more standard features, more advanced capabilities and faster communications than ever before. The Series 0 i control is the industry's most reliable system with a Mean Time Between Failure rate of 52 years. The Series 0 i-MODEL F offers more axes, ladders and paths, as well as high-speed auxiliary machine functions and an expanded list of standard features. Additional features available on the Series 0 i-MODEL F include 15' display, QWERTY keyboard, I/O Link i, high-speed rigid tapping, function for loader control, tolerance control, axis name expansion, program folder management, quick program restart, flexible path axis assignment, multi-path PMC function, ladder dividing management, EtherNet/IP and PROFINET. Optimized Speed The Series 0 i-MODEL F features a suite of advanced motion control software functions to reduce cycle times while enhancing part accuracy and extending machine life.
32-Alphanumeric Character Program Names The Series 0 i-F now allows program names with up to 32 alphanumeric characters so it is compatible with Series 30 i-B. High-Response Vector Control High-Response Vector control (HRV 3) is a high-speed DSP, digital servo and spindle current-control method that provides greater precision and allows for higher machining speeds. Bell-Shaped Acc/Dec Bell-shaped acc/dec minimizes machine shock and reduces the time it takes to accelerate and decelerate and can be applied to rapid, contouring and tapping motions.
AI Contour Control AI Contour Control (AICC I/AICC II) uses advanced look-ahead algorithms to determine the optimal feedrate and acceleration. This can reduce cycle times and improve accuracy, which is especially beneficial when machining complex, curved surfaces such as aerospace or automotive parts or metal dies. Tool Retract & Recover Tool retract and recover simplifies tool inspection and replacement while machining. When activated, the tool safely retracts from the part and then can be manually moved to an inspection position. When released, the tool moves back along the path created by the manual moves. Path Synchronization M-codes are used to make one path wait for the other path to complete an operation before proceeding. One path can also be commanded to wait until another path reaches a specified absolute coordinate position before continuing.
Fanuc Series 0i -md 0i -md
Twin Table Control Twin Table Control adds flexibility for twin-table machining centers and routers. The movement of each table can be synchronized to act as one large table, or managed independently for complex production runs. Program Restart Program restart allows mid-program startup when the program was interrupted for a tool inspection or the machine stopped for a prolonged break.